Fasteners and Machining: Enhancing the Manufacturing Process
Wiki Article
Unveiling the Details of Bolts and Machining Procedures for Optimum Performance
In the world of design and production, the option of fasteners and the complexities of machining processes play a pivotal function in identifying the supreme performance and longevity of a product. From the relatively straightforward job of picking the ideal kind of fastener to the complex precision machining techniques utilized, every step in this procedure needs meticulous attention to detail. As we begin on this expedition into the world of bolts and machining, we will certainly reveal the subtle yet vital variables that can substantially affect the effectiveness and quality of the final product, clarifying the often forgotten aspects that can make all the difference in accomplishing ideal efficiency.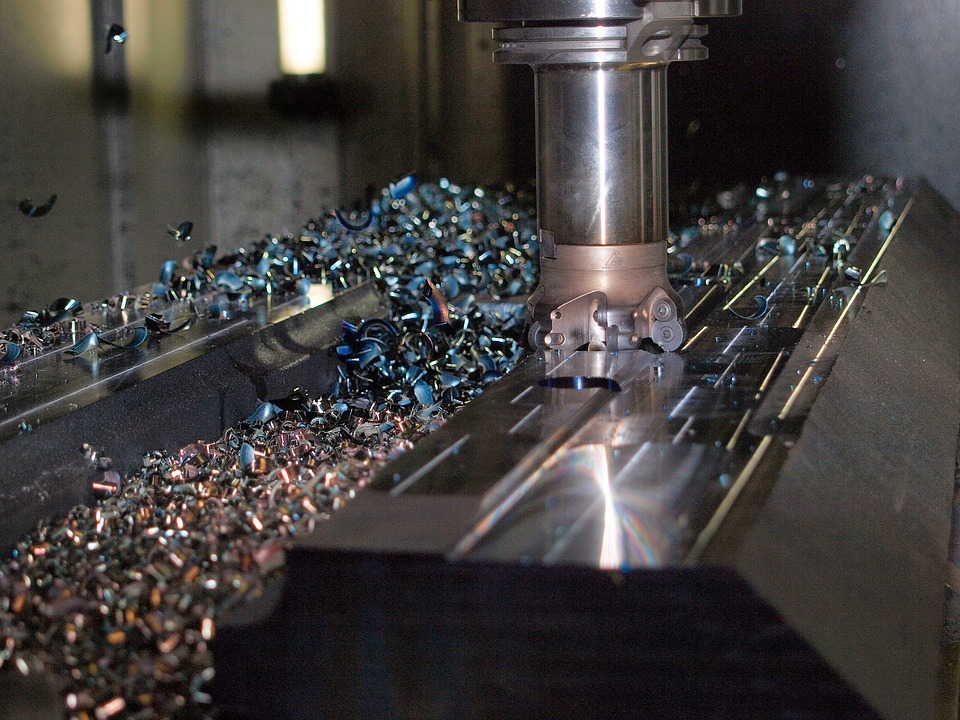
Value of Proper Fastener Option
Picking the ideal bolts is crucial in making certain the structural stability and durability of any kind of mechanical assembly. Bolts play a basic role in holding components with each other securely, with the ideal selection adding significantly to the overall performance and integrity of the setting up. When picking bolts, elements such as material compatibility, environmental conditions, load-bearing ability, and convenience of installment have to be very carefully taken into consideration to assure ideal performance.Improper bolt option can bring about a variety of problems, consisting of loosening, corrosion, and even structural failing. Making use of bolts that are not fit to the specific demands of the assembly can compromise its performance and present safety dangers. Therefore, designers and designers should carefully examine the application requires and select fasteners that satisfy or exceed the required standards and specs.
In addition, the right bolt option process entails examining the joint design, prepared for loads, vibration levels, and potential thermal expansion or contraction to ensure that the selected bolts can stand up to the operating conditions successfully. By prioritizing proper fastener selection, makers can boost the top quality, toughness, and performance of their mechanical settings up.
Types and Features of Bolts
A crucial aspect of mechanical assemblies lies in recognizing the diverse types and one-of-a-kind features of fasteners made use of in different industrial applications. Bolts are vital components that hold structures with each other, making certain stability and capability.Screws are threaded fasteners that are frequently used to join 2 or even more elements together. Bolts are comparable to screws yet are commonly made use of with a nut to produce a secure joint. Nuts are inside threaded bolts that mate with screws to hold components with each other. Washers are slim plates that distribute the load of a fastener, stopping damages to the product being fastened. Rivets are irreversible bolts that are hammered or pressed right into area. Pins are used for alignment or to safeguard parts briefly.
Recognizing the qualities of each type of bolt is vital for choosing the right one for a specific application, making certain optimal performance and integrity of the mechanical setting up. Fasteners and Machining.
Precision Machining Techniques for Effectiveness
The elaborate design needs of different bolts necessitate employing precision machining methods for ideal performance in making procedures. One of the key techniques used in accuracy machining is Computer Numerical Control (CNC) machining, which enables high levels of accuracy and repeatability in the production of bolts.By using precision machining strategies, makers can improve the quality of fasteners, minimize product waste, and improve general manufacturing performance. The usage of advanced machining procedures helps make certain that fasteners blog here fulfill sector criteria and consumer expectations for performance and reliability.

Variables Affecting Machining Process Performance
Various variables play a substantial role in identifying the efficiency of machining procedures in the manufacturing of bolts. Maximizing these criteria based on the certain needs of the bolt being produced is crucial to achieving cost-effective and exact machining.Maker strength and stability likewise play a critical role in determining machining procedure efficiency. A steady equipment with minimal vibrations can improve precision and prevent tool wear, leading to far better total performance. Moreover, the skill and experience of the equipment operator can not be ignored. An educated driver can make real-time modifications, troubleshoot concerns successfully, and ensure that the machining procedure runs efficiently, eventually impacting the final quality of the bolt.

Quality Assurance Steps in Manufacturing
Aspects affecting machining procedure efficiency, such as reducing tool selection and device stability, straight influence the execution of top quality control measures in production. Quality assurance measures are necessary in view ensuring that items fulfill the needed standards and specifications. In the manufacturing process, numerous techniques are used to keep high quality requirements. Examination and testing play an essential duty in identifying any type of inconsistencies from the wanted outcome. Routine maintenance of machining devices is likewise crucial to support high quality control. Calibration of tools and devices is necessary to guarantee precise and exact production procedures. In addition, carrying out standard operating procedures and methods can aid in keeping consistency and top quality throughout the manufacturing line. Quality assurance determines not just concentrate on the end product yet additionally on every stage of the manufacturing procedure to avoid mistakes and problems. By sticking to stringent high quality control measures, suppliers can improve customer satisfaction, build a track record for reliability, and inevitably accomplish optimum performance in their machining procedures.Final Thought
Finally, selecting the right fasteners and using accuracy machining strategies are vital for optimum performance in manufacturing procedures. Understanding the kinds and qualities of fasteners, in addition to aspects affecting machining process efficiency, can cause enhanced effectiveness and high quality control procedures. By taking notice of these ins and outs, producers can achieve greater degrees of performance and dependability in their items.In the realm of engineering and production, the selection of bolts and the details of machining processes play a pivotal duty in identifying the ultimate performance and toughness of a product (Fasteners and Machining). One of the primary strategies utilized in accuracy machining is Computer system Numerical Control (CNC) machining, which makes it possible for high degrees of accuracy and repeatability in the manufacturing of fasteners. The usage of innovative machining processes helps make sure that fasteners satisfy sector standards and consumer assumptions for performance and dependability
In final thought, picking the right bolts and making use of precision machining strategies are necessary for click for info optimal efficiency in manufacturing procedures. Recognizing the types and features of bolts, along with factors affecting machining process performance, can lead to improved performance and quality control measures.
Report this wiki page